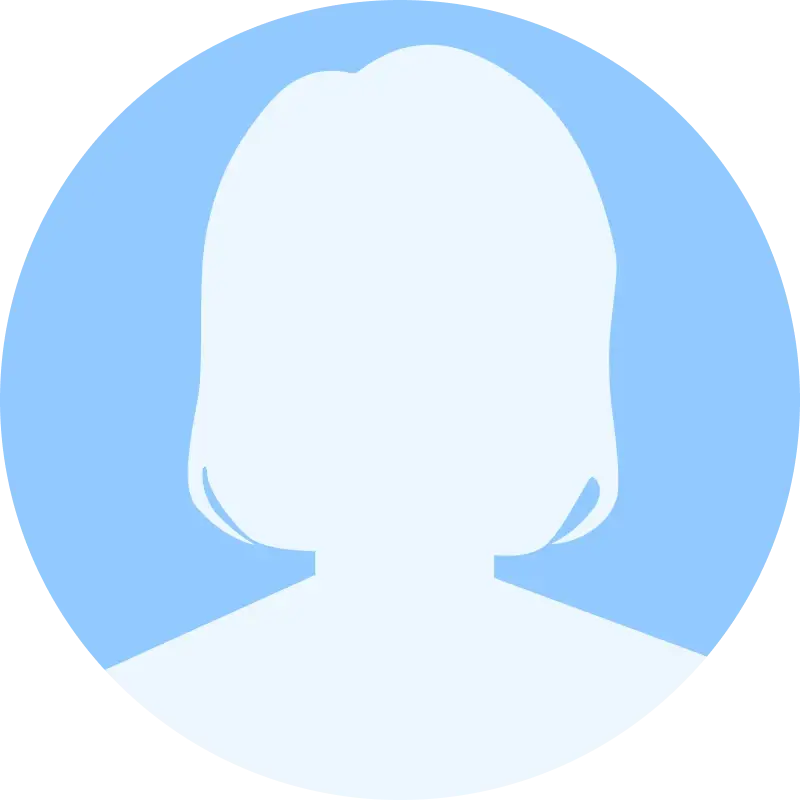
The manufacturing industry is facing a skilled labor shortage, and this has become a major challenge for companies in the industry. In this article, we will explore the causes of the skilled labor shortage in the manufacturing industry, look at the impact of this shortage, and explore effective strategies for addressing this issue.
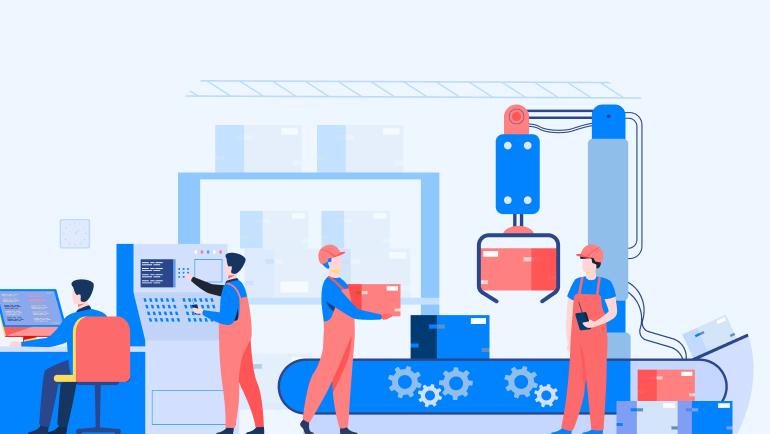
Skilled Labor Shortage in Manufacturing: An Overview
As the wheels of industrialization continue to turn, the manufacturing sector is faced with a growing challenge – a skilled labor shortage in the manufacturing industry. Inflation, concerns about a possible recession, and problems in the supply chain are other challenges at the top of the list in the industry. But while these issues are short-term concerns, the skilled labor shortage in manufacturing is not likely to be solved in the long term without prompt action, according to the National Association of Manufacturers.
The manufacturing industry requires workers with a range of specialized skills, including knowledge of robotics, automation, engineering, programming, and other technical skills. While the need for machines and automation has increased over the years, the demand for skilled workers to operate and maintain these machines has not been met.
The result? A widening gap between the number of available job openings that require specialized skills and the number of workers who possess these skills. According to a study on labor statistics, the manufacturing skills gap could result in 2.1 million unfilled jobs by 2030 in the U.S. alone.
As the manufacturing industry struggles with skilled talent shortage, the question arises – how can the manufacturing sector attract and retain skilled workers to ensure growth and sustainability?
8 Reasons for the Skilled Labor Shortage in Manufacturing
While the COVID-19 pandemic made it harder for manufacturing organizations to find and keep the talent they need to satisfy production expectations, there was a severe shortage in the global labor market in the manufacturing sector long before the pandemic hit. In fact, a 2018 study estimated that more than 8 million manufacturing jobs could go unfulfilled globally by 2030. Let’s explore the reasons behind the labor shortage in manufacturing.
1. Ageing workforce
As the baby boomer generation approaches retirement age, many skilled and experienced experts are leaving the manufacturing industry. One in four American workers, 20% of UK workers, and 22% of Canadian workers are over 55 and employed in the industrial sector, according to statistics. 30% of the manufacturing workforce in South Korea is above 50. The loss of important knowledge, expertise and skills plays a big role in the manufacturing skills shortage. It is also getting harder to find workers who have the skills and credentials needed to fill open positions.
2. Low wages
A candidate-driven job market has emerged because of the persistent skilled labor shortage in the manufacturing industry. Most of today's labor force is calling for wage increases. After all, monetary compensation is usually the driving force behind a career switch. According to a report by the National Employment Law Project, 53% of frontline production workers in manufacturing earn less than $15 per hour. This makes it difficult for manufacturing organizations to attract and retain skilled workers.
3. Lack of training opportunities
With the rapid advancement of technology, the skills required to work in manufacturing are constantly evolving. However, many workers do not have access to the training they need to keep up with these changes. According to a 2018 report by Deloitte and the Manufacturing Institute, only 36% of manufacturing organizations have an upskilling program in place for their workers.
Learn More: The Importance of Workforce Collaboration in 2023
4. Negative perceptions of the industry
The jobs in the manufacturing industry are generally perceived as low paying, physically demanding, and not advanced technologically. This negative perception has led to a lack of interest in manufacturing jobs among younger generations. According to a report by the National Association of Manufacturers, only 27% of parents encourage their child to pursue a career in manufacturing.
5. Technological advancements
While the increasing use of automation and robotics in manufacturing has reduced the number of workers needed to perform certain tasks, it has also created a need for workers with specialized skills to operate and maintain these machines. According to a report by the Brookings Institution, 82% of manufacturing executives say that a shortage of workers with the necessary skills is impacting their ability to implement new technologies.
6. Lack of flexible work options
One of the biggest problems in the manufacturing industry is that there aren't many ways to work flexibly. Many workers have learned from the pandemic how important it is to keep a good balance between work and life. In fact, Randstad Employer Brand Research report found that work-life balance is the second most important reason for employees to change jobs.
Learn More: Types of Flexible Work Arrangements
7. Mental health issues
Manufacturing jobs can be physically demanding, with high-stress, which can lead to mental health issues such as depression, anxiety, and substance abuse. According to a study, manufacturing workers have a higher risk of developing mental health problems than workers in many other industries. Manufacturing workers encountered a variety of difficulties during the pandemic. Due to workforce shortages and customer demands, some businesses experienced repeated shutdowns and brief layoffs, while others asked workers to put in long hours. A research found that burnout increased by 86% among workers in the manufacturing sector in 2020.
8. Lack of diversity
The lack of diversity in the manufacturing workforce, especially when it comes to gender equality, has been a problem for many years. Even though the industry has made a lot of progress to make the workplace more diverse, studies show that women make up less than 30% of the manufacturing workforce around the world. More needs to be done to get women to work in the field. For example, manufacturing organizations need to look at the jobs they offer and make changes to their workplaces so that they can hire a range of people to do the job.
Learn More: How to Make Diversity, Equity, and Inclusion (DEI) a Reality in Hybrid Work
5 Major Impacts of the Skilled Labor Shortage in the Manufacturing Industry
The skilled labor shortage in manufacturing has far-reaching implications for the industry and the wider economy, from reduced productivity and output to increased labor costs and reduced competitiveness. Let’s explore in more detail the various impacts of the skilled labor shortage on the manufacturing industry.
1. Reduced productivity and output
The skilled labor shortage in the manufacturing industry translates to a lack of workers with the technical skills and experience needed to operate machinery and perform other specialized tasks. This can result in lower productivity and reduced output, which can lead to lost business and lower revenues. According to a survey, 78% of manufacturing organizations report a moderate to severe shortage of skilled workers, and 69% say that the shortage has negatively impacted their ability to meet customer demand.
2. Increased labor costs
The shortage of skilled workers in manufacturing can result in a demand for higher wages and benefits from existing workers, as manufacturing organizations compete for a limited pool of qualified candidates. This can increase labor costs and reduce profit margins. According to a report, 72.9% of manufacturing organizations cite rising labor costs as a business challenge.
3. Lack of innovation
Skilled workers are often essential for developing and implementing new manufacturing technologies and processes. Without enough skilled workers, manufacturing organizations may struggle to innovate and keep up with industry trends. According to a survey by PwC, 70% of manufacturing organizations cite the lack of skilled workers as a major barrier to innovation.
4. Safety risks
When manufacturing organizations are short-staffed, workers may be asked to take on additional responsibilities or work longer hours, which can increase the risk of accidents and injuries. According to a report, the manufacturing industry has one of the highest rates of nonfatal occupational injuries and illnesses. Employees who aren't trained or who have too much work to do are more likely to make mistakes. This opens the door to problems with the quality of the products and to bigger problems like product recalls and lawsuits.
5. Skills gaps
When there are not enough skilled workers available, manufacturing organizations may need to hire less-skilled workers or invest in training programs for existing employees. This can lead to skills gaps in the workforce, which can further reduce productivity and output.
Learn More: Is the Metaverse Workplace the Future of Work?
11 Solutions for the Skilled Labor Shortage in the Manufacturing Industry
The skilled labor shortage in manufacturing is a complex issue that requires a multi-faceted approach to address. While there is no one-size-fits-all solution to the shortage, there are several strategies that can be implemented to mitigate its impact and attract more skilled workers to the industry. Let’s find out.
1. Improve working conditions
Improving working conditions, such as increasing pay and benefits, can help companies attract and retain workers in the manufacturing industry. According to a report by the National Bureau of Economic Research, a 10% increase in wages can lead to a 3-5% increase in worker productivity. Providing training and development opportunities can also improve job satisfaction and retention rates.
2. Expand your recruitment pool
Work with the high schools in your area to show students what a career in manufacturing might look like. Get their attention and show them that making things is a good option when they are thinking about what to do after school. Also, think about how the demographics of your workforce compare to the demographics of your community. For example, there aren't enough women in manufacturing. Increasing the participation of women and other underrepresented groups in the manufacturing industry can help address the skilled labor shortage. Providing support and mentorship programs can also help retain these workers. For example, the Women in Manufacturing Association offers networking and professional development opportunities for women in the manufacturing industry.
Learn More: Refine Your Recruitment Process to Attract the Best Talent
3. Upskilling and reskilling
To overcome the shortage of skilled labor in manufacturing, HR in the sector must make a concentrated effort to develop the skill sets needed by the workforce internally, which many are doing by investing in the growth of their current staff. According to a poll, 63% of manufacturing organizations are currently retraining employees, while another 60% are cross training their workforce. Upskilling and reskilling programs provide an opportunity for workers to acquire new skills that are relevant to emerging technologies and changing roles in the manufacturing industry. Such programs can also be implemented in partnership with educational institutions, training providers, and industry associations. According to a report by Deloitte, 70% of manufacturing executives believe that their company's productivity and profitability would improve if employees were upskilled or reskilled.
4. Invest in workforce retention and engagement
Improving employee engagement and retention is vital to address the skilled labor shortage in the manufacturing industry. Manufacturing organizations can focus on providing flexible working hours and a good work-life balance. Another good way to keep employees engaged is by providing opportunities for retraining and advancement, as well as task variability. Providing opportunities for skill development and creating a culture of learning, creating a positive work environment, regular communication, recognition, and benefits can also improve engagement and retention.
Learn More: 70 Ways to Improve Employee Engagement for HR
5. Invest in technology the right way
To lessen the effects of the skilled labor shortage in the coming years, HR in manufacturing will have to do more than attract new talent. It will also have to invest in technology. Manufacturing organizations that are willing to invest in new equipment and better integration of the Internet of Things (IoT), robotics, 5G, edge computing, artificial intelligence, and other technologies find that their products are made faster, better, with less waste, and less labor. By teaching machine operators how to use the new equipment, they are pushed to work smarter, not necessarily harder. They also take on more responsibility and sometimes even get a raise for their new skills. The adoption of technology can also help address the skilled labor shortage in the manufacturing industry by automating repetitive and manual tasks, allowing workers to focus on more complex tasks. This can also attract younger workers who are more comfortable with technology.
6. Provide flexible work options (wherever possible)
Adopting flexible work arrangements, such as remote work and flexible schedules, can help attract and retain workers in the manufacturing industry. According to a survey by PwC, 71% of manufacturing executives believe that flexible work arrangements can help address the skilled labor shortage. In addition, offering flexible work arrangements can improve work-life balance and job satisfaction for workers. Manufacturing organizations should try to accommodate flexible working arrangements. One obvious example is letting people work from home. A digitally transformed company can enable a wide range of remote workers. They can be knowledge workers, office managers, engineers, technicians, or even equipment operators from anywhere in the world with an Internet connection.
Learn More: Why the Manufacturing Sector Should Prioritize Digital HR in 2023
7. Undertake training initiatives
Businesses in the manufacturing industry can make sure that their employees have the skills and knowledge necessary to do their work successfully. Using Augmented Reality (AR)-based training programs, employees can receive hands-on instruction that enables them to practice in a safe environment before engaging in real-world operations. By doing this, the training might be more effective, and the amount of extra labor needed to manage and train new workers might be reduced.
8. Provide vocational training
By encouraging and supporting vocational education, a pool of competent workers for the industrial industry can be established. Manufacturing organizations can therefore ensure that there is a steady supply of qualified workers available to fill open positions and meet industry demand. Promoting vocational education is an effective way to attract more workers to the manufacturing industry. In Germany, for example, the dual vocational education system combines theoretical training with practical work experience, resulting in a highly skilled workforce. According to the German Federal Ministry of Education and Research, this system provides an efficient and cost-effective way to meet the demand for skilled workers in various industries, including manufacturing. Other countries, such as Switzerland and Austria, have also implemented successful vocational education systems.
9. Offer Apprenticeships
Offering apprenticeships is another effective way to address the skilled labor shortage in the manufacturing industry. Apprenticeships provide a combination of on-the-job training and classroom instruction, allowing workers to acquire the skills and knowledge needed to succeed in the industry. According to the US Department of Labor, apprenticeships can increase worker productivity and retention rates, while also reducing recruitment costs. In addition, offering apprenticeships can help manufacturing organizations develop a pipeline of skilled workers and address the aging workforce.
10. Use alternative hiring sources
The competition for talent is only going to get tougher, so manufacturing organizations must do everything they can to increase their talent pool. This should include actively looking for skilled people from non-traditional or alternative sources. Many manufacturing organizations are already doing this, according to a survey. For example, 62% of them have hired people with disabilities or special needs or have thought about doing so. Another 56% are looking for retirees, and 52% are thinking about hiring people who have been previously incarcerated.
11. Work on improving perception
Manufacturing organizations can address the negative perception of the industry by highlighting the opportunities for career growth, the use of advanced technologies, and the contribution to the economy. In addition, providing opportunities for community engagement and volunteering can improve the image of the industry.
Learn More: The Future of AI in HR: How HR Tech is Evolving
The Way Forward
The skilled labor shortage is an ongoing challenge for the manufacturing industry, but by implementing effective strategies and being proactive, HR leaders in the manufacturing sector can mitigate the impact of this issue. Implementing the strategies discussed can help HR in manufacturing address this challenge and build a skilled workforce for the future.
By collaborating with educational institutions, offering apprenticeships, adopting flexible work arrangements, addressing perceptions of the industry, and creating a culture of learning, manufacturing organizations can attract and retain top talent. Additionally, improving employee engagement and retention through regular communication, recognition, and benefits can further support a skilled workforce.
As the manufacturing industry continues to evolve and adapt, it is important to prioritize solutions to the skilled labor shortage to ensure long-term success. By doing so, manufacturing organizations can remain competitive and continue to drive innovation and growth.
Find out how Darwinbox can help you manage the skilled labor shortage for your manufacturing company, book a demo today!
Speak Your Mind