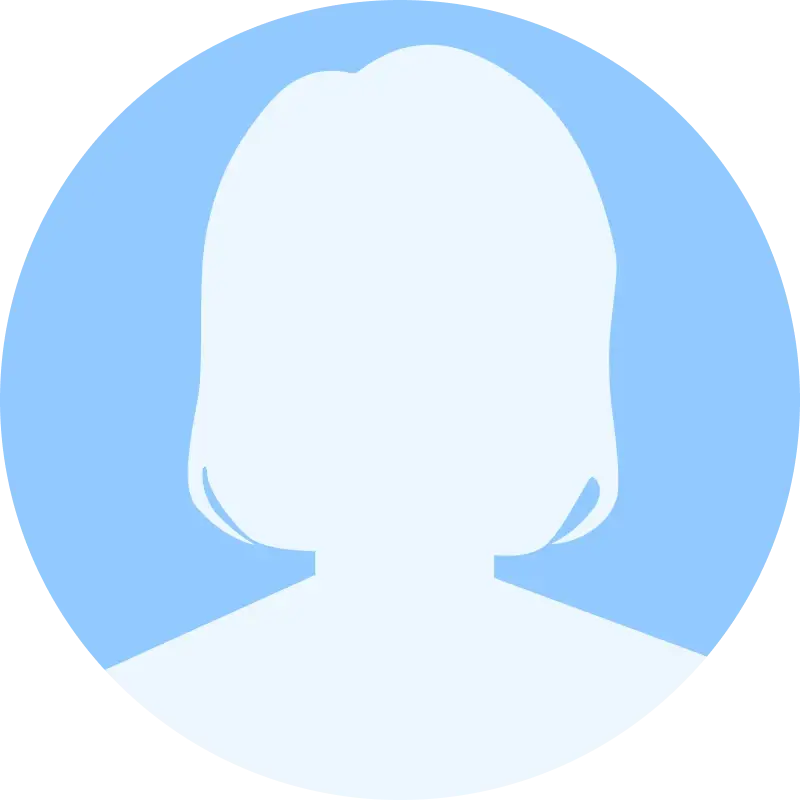
As the manufacturing sector continues to evolve and embrace digital transformation, digital HR is becoming an essential tool for managing HR processes. In this article, we will explore the critical role HR Tech will play in driving success in the manufacturing sector in 2023.
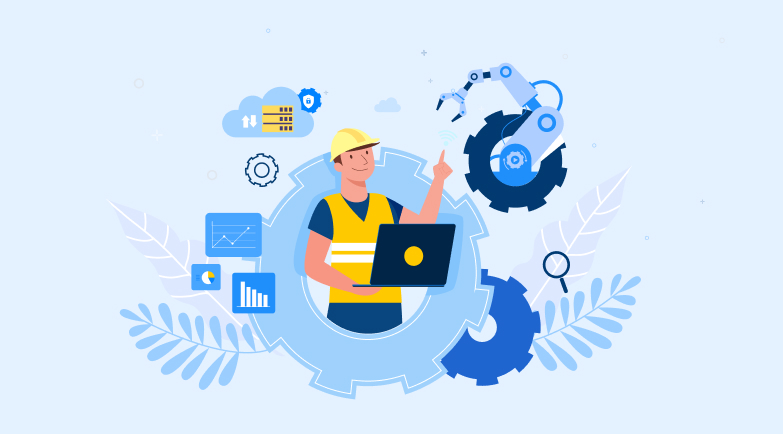
Table of Contents
The Manufacturing Sector: An Overview
The manufacturing sector has been a key contributor to the global economy for centuries, and it remains essential for the continued growth and development of emerging economies. The industry has evolved rapidly over the years, with technological advancements leading to greater efficiency and productivity. However, while all economic sectors suffered during the COVID-19 pandemic, the manufacturing industry suffered significantly because of the labor-intensive nature of its operations.
Due to the global pandemic, the manufacturing sector witnessed disrupted global supply chains, reduced demand for products, labor shortages, and an accelerated pace of adoption of digital technologies. However, even before the coronavirus shook up the world economy, the manufacturing sector was having trouble finding enough workers. In fact, Deloitte and the Manufacturing Institute said in a 2018 study that a tight job market and a lack of people with the right skills could leave as many as 2.4 million factory jobs open until 2028. These challenges have forced manufacturers to adapt and innovate to remain competitive.
Digital Transformation in the Manufacturing Industry
To keep up with change, every industry must embrace digitization, particularly in these turbulent times. Growing digitization enables companies to adapt and create ground-breaking solutions that change entire industries. The manufacturing industry is no exception, it needs to move quickly to incorporate digital solutions to transform how it functions. By implementing digital technologies, the manufacturing industry may improve communication between producers, suppliers, and customers to effectively address some of its most apparent inefficiencies.
The manufacturing sector has historically been hesitant to implement rapid change; thus, digital transformation has not prevailed in every aspect of manufacturing. The objectives established by the industry in response to shifting supply/demand dynamics continue to be rooted in tradition, with more cutting-edge initiatives only being implemented when necessary. Nonetheless, even though disruptions continue to plague the business, the sector is embracing digital change.
36% of CIOs in heavy manufacturing who suffered disruptions reported lower operating cost competitiveness, which can be crippling in such a highly crowded market. Many organizations that were hesitant to make investments in cutting-edge technologies now see digital technologies as the answer to these growing problems.
HR Digital Transformation in the Manufacturing Sector
The role of HR in the manufacturing sector has undergone significant changes in recent years. HR professionals are no longer limited to administrative tasks but are actively involved in developing and implementing talent strategies, leveraging data analytics for decision-making, managing compliance and risk, and fostering collaboration among remote employees. As the manufacturing sector evolves, HR will continue to play a critical role in driving business outcomes and creating a positive employee experience. With the evolving role of HR, the configuration of HR functions has also evolved. Digital HR has proliferated in the manufacturing sector in recent years.
With the emergence of new technologies and the increasing focus on HR digital transformation, digital HR has become an essential tool for managing HR processes and optimizing workforce outcomes. The COVID-19 pandemic has also accelerated the adoption of digital HR in the manufacturing sector. As the manufacturing sector evolves, HR Tech will continue to prove itself as a critical tool for optimizing HR processes, improving workforce outcomes, and driving business success.
Let’s explore how HR Tech can help the manufacturing sector conquer HR challenges in 2023.
Learn More: Key IT Strategy & Implementation Best Practices for an HR Digital Transformation
Challenges in the Manufacturing Industry and How HR Tech Can Help
HR has traditionally played a significant role in the manufacturing industry, and with the recent advancements in technology, digital HR has emerged as a game-changer for the manufacturing sector. This section will provide an in-depth analysis of why the manufacturing sector should adopt digital HR in 2023.
1. Changed worker expectations
Not only did consumer needs shift during the pandemic, but also workers' needs, especially when it comes to working from home. During the pandemic, employers had to find ways for people to work from home or in a hybrid way. Now that the effects of the pandemic have worn off, workers don't want to go back to how things used to be. There are many good things about remote and hybrid work models, such as 74% of workers say that being able to work from home makes them less likely to leave their job, 77% of people who work from home say they are more productive when they do so, and 73% of workers say that being able to work from home has helped them keep a good balance between work and life.
Even though the benefits to employees are clear, it may not seem possible to make remote work a permanent option in the manufacturing industry. But if you look at your employees by their roles, it may not be impossible for some of them to work from home. An HR tech solution can:
- Carefully analyze each job in the company to see which skills and responsibilities can be done from home.
- Enable real-time monitoring- this kind of technology is essential for people to be able to work from home. Whether they are keeping an eye on production, output, or the health of a machine, off-site workers need real-time data to make good decisions.
- Help configure flexible strategies like shorter shifts, flexible shift options, and making it possible to work part-time.
Workers today want to have a lot of freedom at work. In fact, a recent Employer Brand Research Global Report found that workers rank a good balance between work and life as the second most important reason for looking for a new job. Employers need to find ways to give their workers more freedom at work, especially for jobs that can be done from home.
2. Demand for digital skills
Digital technology has been used in manufacturing for decades, but COVID-19 seems to be pushing many companies to invest a lot more in technology. As the manufacturing industry continues to need more and more technology, it will also need more and more skilled workers. Unfortunately, many manufacturers could be hurt by the growing skills gap. It is 36% harder to hire people with manufacturing skills now than it was in 2018.
This is partly because digital skills are in high demand. Manufacturing organizations can solve this problem by taking the following steps:
A. Undertake an evaluation of skills
The first step in finding skilled workers is to figure out exactly what kinds of skills your company needs now and in the future. Take the time to do a thorough skills assessment so you can find out what skills are needed for each job and what skills your company is likely to need in the years to come.
B. Create a steady flow of talent
Taking action now is the most important thing you can do to deal with the growing skills gap. An HR tech solution can help you get started on building a skills repository/inventory and a pipeline of talent for different jobs in your company.
C. Offer fair salary packages
Randstad Employer Brand Research shows that competitive pay is still the most important factor for job seekers. Make sure that the wages you offer are in line with the norms of the industry.
3. Need For upskilling and reskilling
Many manufacturing organizations are realizing that they can't just rely on hire-for-skills strategies to get the workers they need. At least some of these companies are putting more effort into training and retraining their current employees. It's important that the people you employ have all the tools, resources, and skills they need to do their jobs well. To make this happen, training should begin at onboarding. If you don't already have a structured process for getting new employees up to speed, now is the time to make one.
Upskilling is training that helps your employees move up the career ladder, while reskilling is training that helps them change careers. Most of the time, retraining doesn't lead to promotions. Instead, you use retraining to help your current employees get the skills they need to stay employed in the future. For example, giving your employees digital or forklift certification training will give them the skills they need to keep working on the plant floor as your company becomes more automated.
How HR Tech Can Help
Manufacturing organizations can opt for automated, AI and ML-enabled recruitment and separation to facilitate efficient onboarding and exit processes. HR Tech can help in upskilling and reskilling by providing employees with access to online learning platforms, training materials, and development resources. Additionally, HR Tech can help to identify skill gaps and to provide training plans that are tailored to each employee's unique needs and goals. By leveraging HR Tech for upskilling and reskilling, organizations can ensure that their employees have the skills and knowledge they need to stay competitive in today's rapidly changing business environment.
Learn More: The Future of AI in HR: How HR Tech is Evolving
4. Ageing workforce
Many employers have been worried about an ageing workforce for a long time, especially those in the manufacturing industry who need to keep up with production despite a shrinking pool of workers. If your business hasn't already felt the effects of an ageing workforce, it will soon. By 2030, in fact: the first baby boomers will turn 85, the first Gen Xers will turn 65, and the first Millennials will turn 50. Manufacturers all over the world must take steps right now to improve how they hire and keep employees, but they should also take advantage of the skills and experience of these older workers before they start to leave the workforce.
You could train older workers to run machines that are more complex but require less physical effort. By taking this step, you can keep these workers' skills and experience in your organization for a longer time. Mentorship programs can be created to help these employees share their skills and knowledge. Finally, with the right training, seniors can continue to work for an appreciable time. An employee training management tool can come in handy to solve this challenge.
5. Shortage of Workforce
The manufacturing workforce is declining for a number of reasons, such as the dearth of STEM-educated graduates, the unfair and outdated perception that suggests that these jobs are not safe, hygienic, or progressive. Additionally, there is a misconception held by some younger generations that the manufacturing industry does not offer competitive wages, innovation, or sophistication. The industry's robust and consistent financial development seems to have escaped notice.
HR leaders must act rapidly to address the huge loss in human capital evident across manufacturing, a situation that will only get more urgent over the coming years. The human resources department must discover ways to replace the human capital that every firm needs, as the average age of highly trained workers is 56, and about a quarter of the skilled worker base is expected to retire over the next ten years.
Pay alone isn't enough to make manufacturing the worker magnet it was decades before, despite the industry's average wage of about $77,500 annually being greater than wages in almost any other sector. Manpower shortage is a problem that HR departments in manufacturing must actively try to tackle.
To solve this challenge, HR Tech can support talent pipeline and succession planning by:
- Providing data-driven insights that help organizations identify employees with the skills, competencies, and potential to succeed in future leadership roles.
- Identifying skills gaps and developing targeted training plans that align with an organization's talent strategy.
- Creating a centralized talent database that includes information about employees' skills, competencies, career aspirations, and development needs. This information can be used to identify potential successors for key leadership roles and to create personalized development plans.
- Facilitating career development opportunities for employees, which can help employees build the skills they need to succeed in future leadership roles.
Learn More: Digital Transformation in L&D: A Culture of Innovation & Re-modelling
6. Issues in Recruitment
Hiring issues in the manufacturing industry are, unfortunately, deeply rooted and, in some ways, part of the system as a whole. Because many manufacturing jobs are very specific, like that of highly specialized civil engineers with certain skills and talents, the pool of people who could be qualified is naturally small. The problem is that manufacturing hasn't been able to compete with other industries well enough to consistently fill its workforce needs.
This has been made worse by stagnant recruiting budgets and a lack of focus on college recruitment, especially since college curriculums and graduate expectations have changed a lot. A recent study indicated that 55% of manufacturers acknowledged a significant lack of personnel with the appropriate skill sets in their R&D departments, with comparable numbers in marketing.
To effectively engage with and attract graduates, recruiting in the manufacturing sector needs to be flexible and agile. Candidates will quickly lose interest in an interview process that seems to go on too long – a common practice in manufacturing. HR Tech can dramatically increase recruiting efficiency, particularly when combined with new employee feedback surveys that assist to iteratively improve recruiting and hiring practices.
AI-based HR tools can help make this process smoother by sorting hundreds of resumes using keywords and saving time. Smooth mobile experiences, data-driven pre-selection processes and personalized, AI-based onboarding programs are just a few of the use cases of HR Tech that can solve recruitment issues in the manufacturing sector. Darwinbox helped Vedanta Limited standardize their business processes workflows related to conformation, separation, and transfer movements to solve their recruitment challenges.
7. Attrition and Retention
Keeping highly competent employees within an organization is a very real struggle for most HR departments, regardless of the business. Minimizing attrition is crucial for manufacturing organizations because of the severe limitations in their staff and recruitment capacity. Since employees are naturally tempted to explore new and interesting prospects, the industry is unfortunately prone to high turnover rates.
The modern workforce prospers when employers pay attention to and heed their collective voice. A key element of such a model is feedback. HR Tech can provide an easy-to-use platform that allows managers and employees to share feedback in real-time, which can help to improve communication and collaboration in the workplace. It can help managers analyze feedback data, identify trends, and gain insights into employee sentiment. This can help managers make data-driven decisions about employee development, training, and retention.
HR Tech can facilitate goal-setting and performance tracking, which can help employees to understand their strengths and areas for development, as well as track their progress over time. This can help to improve employee engagement and motivation, as employees feel they are making progress toward their career goals. For instance, Darwinbox equipped Adani Wilmar with role-based dashboards so that HODs and HRBPs have a clear view of every employee’s performance. HRBPs are also able to ensure that self-reviews and manager reviews are done on time and that the process is followed in the right manner.
Finally, HR tech can provide a scheduling option for feedback, which can help managers ensure they are providing regular and timely feedback to their employees. This can help build stronger relationships between managers and employees and promote a culture of continuous improvement, which facilities retention.
Learn More: The 30 Best Employee Feedback examples in 2022
8. Poor Employee Engagement
Gallup research shows that only one in four people who work in manufacturing are engaged.
Hope comes from the fact that 68% of employees that work in manufacturing companies that have earned the title of "Best Place to Work" are very engaged in their jobs. This shows how important it is to invest in and prioritize EX. Despite the fact that manufacturing has added a lot of jobs recently, it hasn't been able to effectively utilize its larger workforce. This is especially hard for HR departments in the manufacturing sector because of the sheer size of the workforce and the fact that employees tend to be spread out over multiple locations and long distances, especially without the right feedback and communication tools. In many businesses, the top leaders may be in a different city, state, or even country than most other employees. The manufacturing sector must significantly increase its capacity to cultivate and create compelling work environments if it is to capitalize on the strength and insight offered by its employees.
Learn More: Top 11 Employee Engagement Tools for 2023
HR Tech can help improve employee engagement in the following ways:
- Communication: HR Tech can provide an easy-to-use platform for managers and employees to communicate, engage, and collaborate.
- Recognition: HR Tech can provide a platform for managers and coworkers to recognize and reward employees for their achievements and contributions. Darwinbox solved low workforce engagement for Aarti Industries by implementing a robust Rewards and Recognition program that included gamified badges and leader board, Nomination Reward Programs, peer-to-peer Recognition, Integrated Rewards Marketplace, and event-based rewards, etc.
- Learning and Development: HR Tech can provide access to learning and development resources, including online courses, training materials, and development plans.
- Surveys and Polls: HR Tech can provide a platform for managers to gather feedback from employees through surveys and polls.
Learn More: 9 Most Effective Employee Communication Tools for 2023
Top 5 Benefits of Adopting Digital HR in Manufacturing
The manufacturing sector is facing increasing pressure to adopt new technologies to remain competitive in today's global economy. One area where technology can have a significant impact is HR. Let’s explore why the manufacturing sector should prioritize HR tech, and the benefits it can provide.
1. Improved Efficiency
One of the primary benefits of HR tech is that it can help to improve efficiency by automating time-consuming HR processes. For example, HR tech can help to automate the recruitment and onboarding process, allowing HR staff to focus on more strategic initiatives. Similarly, HR tech can help to automate payroll, benefits administration, and compliance tasks, reducing the risk of errors and freeing up HR staff to focus on more valuable activities.
2. Reduced Costs
HR tech can also help to reduce costs by eliminating manual processes and reducing errors. For example, manual HR processes such as paper-based record-keeping can be time-consuming and prone to errors. By automating these processes, HR tech can help to reduce the risk of errors and free up HR staff to focus on higher-level tasks. Additionally, HR tech can help manufacturers to identify areas where they can reduce costs, such as by identifying areas where they are overstaffed or where they can optimize scheduling.
3. Enhanced Employee Experience
HR tech can also help to enhance the employee experience by providing employees with greater visibility into their benefits, career development opportunities, and performance feedback. For example, HR tech can provide employees with self-service portals where they can access their pay stubs, benefits information, and training materials. Additionally, HR tech can provide managers with tools to more effectively manage their teams, such as by providing real-time performance feedback and coaching resources.
4. Improved Talent Management
Finally, HR tech can help manufacturers improve their talent management capabilities by providing them with the tools and resources necessary to attract and retain top talent. In today's competitive job market, it is essential for manufacturers to provide a positive employee experience that supports the growth and development of their employees. HR tech can help manufacturers achieve this by providing employees with access to development resources, training opportunities, and career progression paths.
5. Compliance and Risk Management
Compliance and risk management are critical in the manufacturing sector. HR Tech can help manufacturers manage compliance and mitigate risk by automating processes, tracking certifications and training, and providing access to relevant documentation and policies.
The Way Forward
The manufacturing sector can benefit significantly from adopting digital HR solutions. By leveraging digital HR, manufacturers can streamline HR processes, improve operational efficiency, enhance employee engagement, upskill and reskill their workforce, and manage compliance and risk. With the rapid pace of technological advancement, digital HR solutions can help manufacturers remain competitive in the market and attract and retain top talent.
The challenges brought about by the COVID-19 pandemic have also highlighted the importance of digital HR solutions in enabling hybrid work and maintaining business continuity. As such, manufacturers must prioritize digital HR to create a positive employee experience, foster a culture of innovation and agility, and improve business outcomes. The time is now for the manufacturing sector to embrace digital HR and unlock the full potential of their workforce.
Find out how Darwinbox can help you unlock the benefits of digital HR for your manufacturing company, book a demo today!
Speak Your Mind