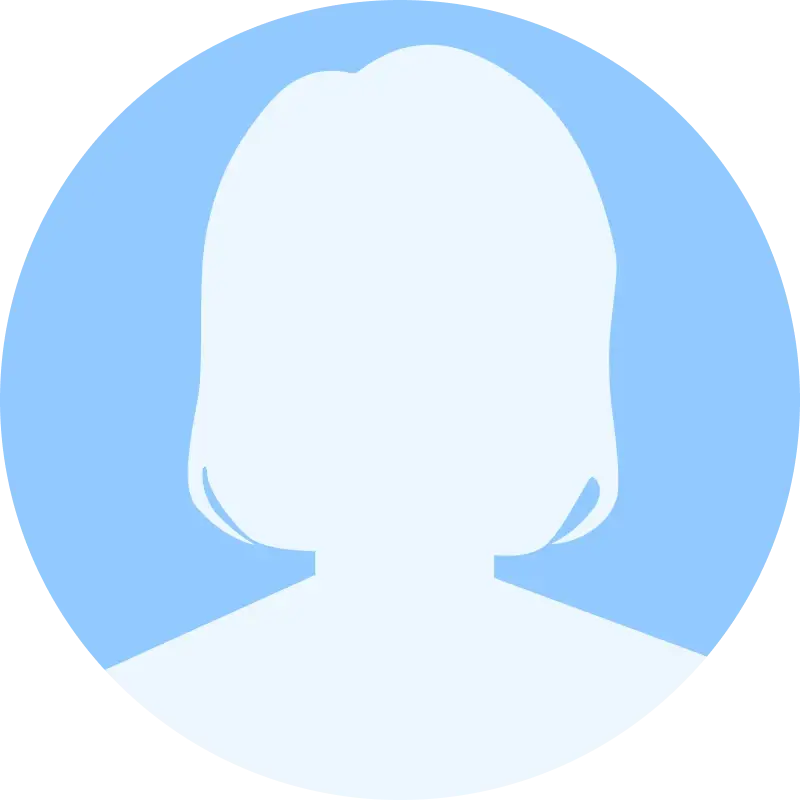
We’re now well into Industry 4.0, and manufacturing companies are fast approaching a state of digitization where the lines between the physical and digital are blurred. It is now the responsibility of the HR leader to decide how humans and machines work together and what the new definition of employee experience will be. This article explains the vital role of human resources in Industry 4.0 and the gradual rise of HR 4.0 to help tackle this change.
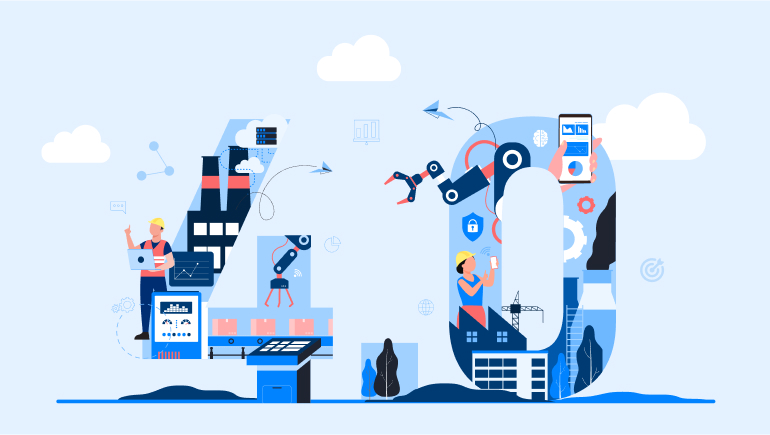
Industry 4.0, or the Fourth Industrial Revolution, is the age where artificial intelligence (AI), the internet of things (IoT), big data analytics, cloud computing, and virtual reality (VR) aren’t just futuristic concepts but are technologies used every day by manufacturing companies.
Industry 4.0 essentially brings in a whole new way of working, and the magnitude, pace, and impacts of this revolution are altering the role of the HR function in the manufacturing sector.
How Will Industry 4.0 Disrupt HR and Shape the Future of HR?
Given that digitization and automation can replace several tasks done by people, particularly in the manufacturing sector, unemployment is one of the biggest fears or challenges posed by Industry 4.0. Yet, this shift from manual labor to using automation and advanced technologies, is one of the most powerful changes that we’re seeing with Industry 4.0.
Consequently, the HR function in a manufacturing company has a vital role to play.
HR professionals must stay informed of Industry 4.0 developments in order to ensure that their employees are in sync with this shift. Human resource management in Industry 4.0 will encompass employee experiences and their engagement with new organizational goals.
How can HR professionals become solution drivers and change agents, as Industry 4.0 practices become the norm?
HR leaders will be responsible for overseeing the people processes that will be altered by the new business models and technologies that come with industry 4.0. The development of new technologies will change the very nature of work and employment, and HR leaders will have to manage the entire process and ensure smooth functioning of companies.
Learn More: Why the Manufacturing Sector Should Prioritize Digital HR in 2023
Key Trends in HR in Industry 4.0
We're seeing a lot of changes in the way manufacturing companies work. Every major technological development and key events that are part of Industry 4.0 will shape the future of the manufacturing industry and how people work at manufacturing companies.
Here are the major trends we’re seeing in the HR world as a result of Industry 4.0:
-
Evolution and change in the kind of jobs at manufacturing companies
As agility and creativity become essential for growth and for companies to have a sustained competitive advantage, technology integration becomes indispensable. The introduction of technology also leads to the development of new business models across all sectors. HR professionals are increasingly required to navigate these shifts.
2. Urgent need for upskilling employees
The new version of manufacturing comes with a new range of skill and talent requirements. HR leaders at manufacturing companies are increasingly focusing on reskilling and upskilling their employees, and making future-focused competency development a mandate for their workforce.
-
Diverse, intergenerational workplaces and greater globalization
Another key HR trend in Industry 4.0 is the emergence of a workforce that is more diverse, intergenerational, and global – a complete contrast to the kind of workforce seen at manufacturing companies in the 1990s. The workforce at most manufacturing companies will, for the first time, consist of employees belonging to five generations, with diverse demographics In addition, the rise of the gig economy and globalization have dissolved organizational and geographical borders, resulting in employees spread across the globe.
4. A focus on employee experience in the workplace
As is the case in several other industries and corporate sectors, there’s increased focus on employee experience and the need for personalized experiences that will help improve employee engagement. Manufacturing companies are also moving away from the one-size-fits-all approach, towards personalization of the employee experience. The introduction of HR technology enables manufacturing companies to understand their new workforce better, and provide them the kind of experience they seek – such as flexible work hours, technology to assist with work, etc.
Learn More: How to Overcome the Skilled Labor Shortage in the Manufacturing Industry
What is the Role of HR in Industry 4.0?
The role of human resources in Industry 4.0 will be a lot more than handling basic HR tasks such as payroll, attendance, etc. HR operations and processes at manufacturing companies will be a lot different going forward.
Here are some of the new tasks HR leaders will take up:
-
Investing in employee experience
Automation and digitalization have had an influence on the employee experience, compelling businesses to manage work in an agile manner. A standard manager-employee relationship that focuses on incentives and rudimentary assistance is no longer sufficient in this context. Employees seek more personalized experiences at work, and prefer to work in organizations that place emphasis on employee engagement, career development, and look at employees as members of the larger team rather than just as people resources doing transactional work.
HR leaders at manufacturing companies must adopt a larger, more holistic perspective when defining, assessing, and establishing the employee experience and the purpose of work.
The kind of workforce, the nature of the work they do, and the way work is being done has changed dramatically. In line with this, HR executives should reimagine the way they approach employee engagement strategy so they can deliver better employee experiences, enhance productivity, and improve employee retention rates..
-
Nurturing a culture of learning
The nature of work in manufacturing companies has changed over the course of Industry 4.0, and there’s the need for employees to acquire new skills, and constantly learn new skills and ensure they’re always prepared to handle the demands of the rapidly-evolving manufacturing industry. . Advancements in technology, work practices, and business structures have created the for continuous learning.
In addition to retraining on technical knowledge for a specialized new job, HR leaders need to focus on ensuring long-term employability of their employees by enhancing abilities that are more generically transferable. The HR function will have to actively take steps to develop and nurture a culture of agile, continuous, digitally-enabled, self-directed, and customized learning. HR leaders must work with workers in the manufacturing sector to educate them on the need for continuous learning and assist them in the learning process.
-
Managing technological change in the workplace
Industry 4.0 is characterized by the adoption of technology, and an evolution of business models, and a change in operations and processes followed at manufacturing companies. Consequently, there’s a change in employment and working models, and the transition to flatter, more interconnected organizational structures. HR leaders must prioritize change management during this time of transition. As more manufacturing companies embrace digital HR transformation, HR leaders must work closely with all stakeholders such as people managers, employees across the board, and labor unions or councils to ensure that they are aware of the changes in the organization and are able to adapt to the new ways of working..
Learn More: A Major HR Challenge: Managing The Millennials
-
Reimagining how HR outcomes and success is measured
HR leaders are often evaluated independently, and HR metrics aren’t part of the overall business metrics. In several manufacturing companies, HR goals and objectives aren’t part of the company’s overall goals.
the HR function has a larger role to play, and human resource management in Industry 4.0 will look quite different from what it did a decade ago. HR objectives are a part of the company’s overall objectives, and organizations track data, and measure the HR team’s performance using success metrics in line with the company’s broader goals.
The International Standards Organization (ISO) has issued a new reporting standard for human capital, creating measures that can be compared. It assesses crucial HR concerns, such as ethics, diversity, leadership, organizational culture and employee wellness, talents and abilities, and succession planning.
5. Making Diversity, Equity, and Inclusion (DEI) a priority
The manufacturing sector is getting increasingly diverse, with people from multiple generations, and across different countries working together. HR leaders in the manufacturing sector have to take this further, to make the industry more diverse. Among the many changes that have come during Industry 4.0 is the fact that organizations have implemented measurable objectives, targets, and mandates to improve diversity. HR leaders are establishing a culture where DEI permeates every aspect of the organization – in hiring, recognition, and performance management – with a focus on altering behaviors, attitudes, and mindsets.
-
Revamp the HR function to be Industry 4.0-ready
Industry 4.0, which has transformed the way manufacturing companies work, is also creating the need for a revamped HR function, with new roles and responsibilities. This requires the leadership to introduce new ways of recruiting skilled workers, adopting HR technology to provide better experiences, and working closely with employees on a regular basis.
As we move ahead in the industrial revolution, we’ll see that every successful manufacturing company will have the following roles in their HR function:
- HR business partner: The HR function is no longer just an ancillary function that might or might not have had a place at the executive table. HR leaders have become more strategic, guiding organizations by identifying and adopting new work methods, driving automation, and facilitating rapid, agile changes.
- People process enabler: The HR leader’s role in empowering others has now become much more important. HR teams are expected to spearhead digital HR transformation and the the digitalization of work, assuming responsibilities for reskilling personnel, and transforming how HR services are delivered.
- Changemaker: The HR team will be responsible for executing and implementing all the strategic changes. From ensuring that all employees adopt technology, preparing the workforce for the needs of the future, to delivering exceptional experiences to employees, HR professionals will lead and manage all the major changes that the future of work in manufacturing will bring in.
- Disruptor: The future of HRM in the manufacturing sector demands that HR leaders also turn disruptors, and lead the innovation race. This involves enhancing existing systems or developing new ones, revolutionizing talent management, and identifying new ways to streamline processes to improve productivity, and focusing on employee engagement to ensure talent retention.
Learn More: Mapping the Evolution of HR in 2023 And Beyond
HR Best Practices You Can Follow During the Next Industrial Revolution
If the Industry 4.0 definition encompasses the ubiquitous use of technology in the workplace and the blurring of lines between the physical and digital, then HR 4.0 is the use of HR technology and automation to people processes.
The digital HR transformation, however, is just beginning. For HR in Industry 4.0 to be able to add value and successfully navigate the new work of manufacturing, the following best practices must be followed:
-
Encourage two-way communication with workers
One of the key features of HR 4.0 must be the redefined relationship between the employer and the employee. HR leaders must work with employees and help them deal with the impact of automation and digitalization on their jobs and operations. HR professionals at manufacturing companies must develop empathy, proactively seek feedback and input from employees, and work with them during this phase of technology adoption and change.
-
Ramp up compliance efforts
As operations and processes change with the adoption of technology, there will be new regulations that companies in the manufacturing sector will have to comply with. For instance, there could be regulations around data privacy for companies that use HR tech for people analytics. or labor laws around workers' rights. When these new rules are implemented, revised, or altered, HR will need to swiftly adapt to these changes.
-
Focus on employee well-being
The industry's disruptions will require HR to play a greater role in providing continuing assistance and ensuring employees' mental and physical well-being. This will include quick grievance resolution, providing personalized assistance, and delivering personalized and seamless employee experiences across the employee lifecycle.
Learn More: 18 Tips to Retain Talent in the Manufacturing Industry
As organizations restructure their business models and reinvent their operations, HR executives will need to adapt and align to the new ways of work. They will have to navigate evolving job roles, skills, and activities, and facilitating strategic workforce planning.
Essentially, human resource management will be completely different from what it has been like over the last few decades.
The use of HR technology will be critical for companies to grow and succeed. Cloud-based, AI-powered HRMS platforms can help your organization establish and implement HR 4.0 practices so you are prepared for the future of work in the manufacturing sector. To learn more, schedule a demo with Darwinbox today!
Speak Your Mind